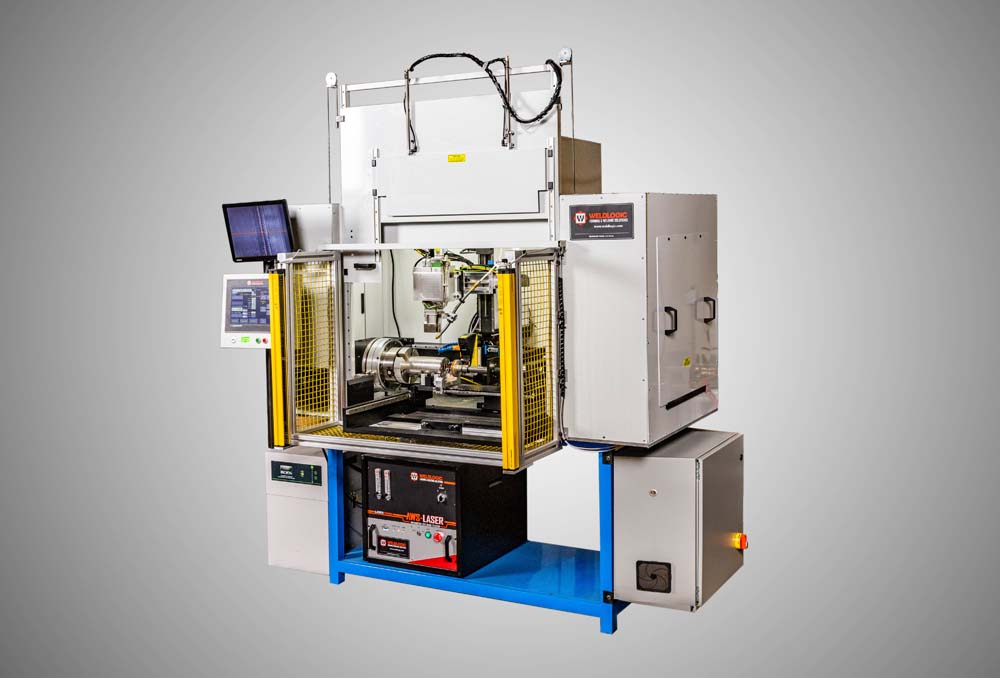
Introduction
Challenge:
Submersible Pump manufacture wanted to replace the decades old resistance welding process used to seam weld thin wall inner tube and outer tube to end caps.
The resistance welding of 4 welds on their pumps produced Low Parts per hour, High Heat input, High Leak Rates, High consumables, and Skills levels.
Solution:
The Pump Manufacture selected Weldlogic to develop and optimize the Laser weld process to enable them to eliminate the resistance welding process and solve many productivity challenges.
Weldlogic Engineers and Process Weld Specialist assessed 4 critical welds required and productivity goals and offered a 3000-Watt Fiber Laser, Beam Oscillation with Automation and Seam Finder/Tracking to eliminate any skill levels and meet productivity goals.
The Weldlogic Laser cell provided Low Heat Input, Low Skill levels, Low Leak Rates, Low Consumables & High Productivity 180 Welds per hour.
Video
Gallery
Features
N/A
Specifications
N/A
Applications
N/A